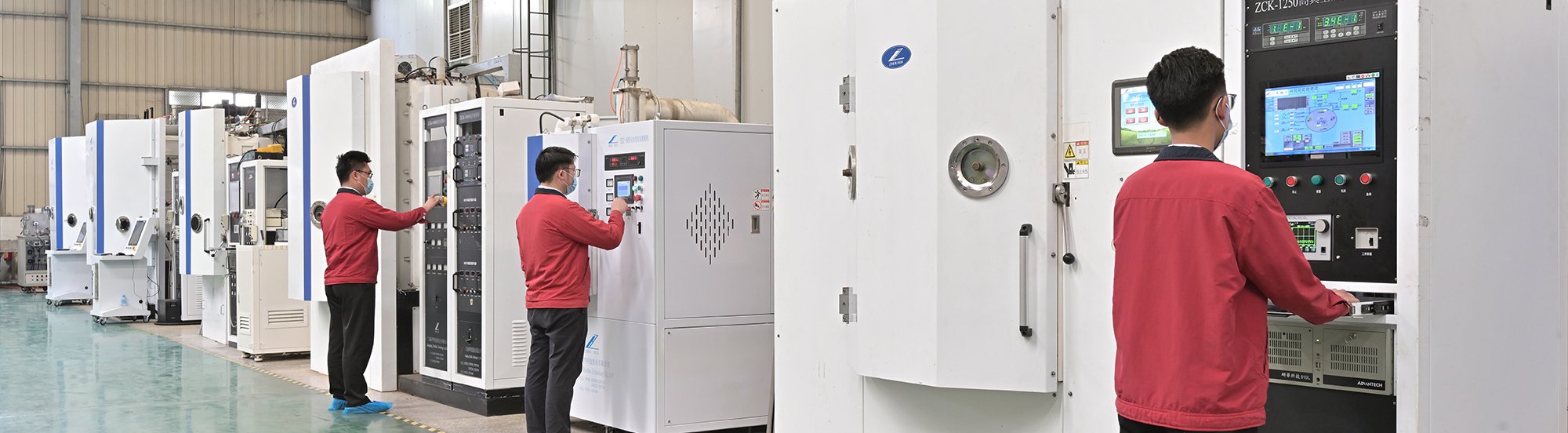
齿轮镀膜技术
PVD沉积技术作为新型表面改性技术已有多年的实践,尤其是真空离子镀技术,在近几年获得了极大的发展,目前已广泛应用在刀具、模具、活塞环、齿轮等部件的处理上。通过真空离子镀技术制备的涂层齿轮可大幅降低摩擦系数,提高耐磨性和一定的耐腐蚀性,已成为齿轮表面强化技术领域研究的重点和热点。

齿轮常用材料主要为锻钢、铸钢、铸铁、有色金属(铜、铝)和塑料。钢材主要有45钢、35SiMn、40Cr、40CrNi、40MnB、38CrMoAl,低碳钢中主要使用20Cr、20CrMnTi、20MnB、20CrMnTo。锻钢由于性能较好,因此在齿轮上应用较广泛,而铸钢通常用于制造齿轮直径>400mm、结构复杂的齿轮。铸铁齿轮抗胶合及抗点蚀能力强,但缺乏抗冲击耐磨性,主要用于工作平稳、功率不大低速或尺寸较大形状复杂时,能在缺少润滑的条件下工作,适于开放式传动。有色金属中常用的是锡青铜、铝铁青铜和铸造铝合金,常用于制造涡轮或齿轮,但滑动性和抗摩擦性能较差,只用于轻、中载荷和中低转速齿轮。非金属材料齿轮主要用于某些具有特殊要求,比如无油润滑、可靠性高。污染小等条件的领域,像家用电器、医疗器械、食品机械和纺织机械等。
齿轮镀膜材料
工程陶瓷材料是极具有开发应用前景的材料,工程陶瓷材料具有高的强度和硬度,尤其具有优良的耐热性,低的热传导性和热膨胀性和以及很高的耐磨性和抗氧化能力。大量的研究表明陶瓷材料本身具有耐热,对金属磨损小等特点。因此,用陶瓷材料代替金属材料作耐磨零件可提高摩擦副的寿命,能满足一些对材料高温和高耐磨,多功能等苛刻要求。当前,工程陶瓷材料已应用于制造发动机耐热件、机械传动中的耐磨件、化工设备中的耐腐蚀件及密封件,日益显示陶瓷材料广泛的应用前景。
各发达国家如德、日、美、英等国家非常重视工程陶瓷材料的开发与应用,竞相投入大量的资金和人力,发展工程陶瓷的加工理论和技术。德国已推出了一个名为“SFB442”的计划,其目的是利用PVD 技术,在零件表面合成适当的薄膜以替代对环境和人体有潜在危害的润滑介质。德国的P.W.Gold等人利用SFB442计划的资金资助,应用PVD技术在滚动轴承的表面沉积薄膜,发现滚动轴承的抗磨性能明显提高,表面沉积的薄膜完全可以替代极压抗磨添加剂的功能。德国的Joachim,Franz等人利用PVD技术制备WC/C薄膜展示了极好的抗疲劳性能,高于含有EP添加剂的润滑油,这个结果同样得出了用涂层替代有害添加剂的可能性。德国亚琛技术大学材料科学学院的E.Lugscheider等人在DFG(GermanResearch Commission)的资助下,在100Cr6钢上利用PVD 技术沉积适当的薄膜后,证明其抗疲劳强度显著提高。另外,美国通用汽车公司已开始在其VolvoS80Turbo 型汽车的齿轮表面沉积薄膜以提高抗疲劳点蚀能力;著名的Timken公司已推出命名为ES200的齿轮表面薄膜;注册商标为MAXIT的齿轮涂层已在德国出现;注册商标分别为Graphit-iC和Dymon-iC的齿轮涂层在英国也已出现。
作为机械传动中的重要零部件,齿轮在工业中具有重要的地位,因此研究陶瓷材料在齿轮上的应用具有非常重要的现实意义。目前,应用于齿轮上的工程陶瓷主要有以下几种。
1 TiN
离子镀TiN陶瓷涂层是目前应用最广泛的一种表面改性涂层,具有高硬度、高粘着强度、低摩擦系数、良好的抗腐蚀性等特点,已广泛应用在各个领域,特别是在刀具、模具行业。影响陶瓷涂层在齿轮上应用的主要原因是陶瓷涂层与基体之间的结合力问题。由于齿轮的工作条件和影响因素远比刀具、模具复杂,致使单一的TiN涂层在齿轮表面处理上的应用受到很大制约。陶瓷涂层虽然具有高硬度、低摩擦系数、耐腐蚀等优点,但脆性大,且难以获得较厚的涂层,故需要硬度高、强度高的基体支撑涂层,才能发挥其特点。所以,陶瓷涂层多用于硬质合金及高速钢表面。而齿轮材料相对于陶瓷材料较软,基体与涂层性质差异较大,因此涂层和基体结合较差,对涂层支持不足,使得涂层在使用过程中容易发生脱落,非但不能发挥陶瓷涂层的优势,反而脱落的陶瓷涂层颗粒会对齿轮造成磨料磨损,加快齿轮的磨损失效。目前的解决方法是采用复合表面处理技术,改善陶瓷与基体间结合力。复合表面处理技术指物理气相沉积涂层与其它表面处理工艺或涂层相结合,采用两种单独的表面/次表面对基体材料表面进行改性,以获得单一表面处理工艺所不能达到的复合机械性能。通过离子氮化和PVD沉积TiN复合涂层是目前研究最多的一种复合涂层,等离子氮化基体与TiN陶瓷复合涂层具有较强的结合力,且耐磨性得到显著提高。
具有优良耐磨性和膜基结合力的TiN膜层的最佳厚度约为3~4μm,若膜层厚度小于2μm,则耐磨性提升不明显;若膜层厚度大于5μm则膜基结合力下降。
2多层、多组元TiN涂层
随着TiN涂层应用的逐渐广泛,对如何改善和提高TiN涂层的研究越来越多。近些年来,人们在二元TiN涂层的基础上研制出了多组元涂层和多层涂层,如Ti-C-N,Ti-C-N-B,Ti-Al-N,Ti-B-N,(Tix,Cr1-x)N,TiN/Al2O3等[10]。通过向TiN涂层中添加Al、Si等元素,可以提高涂层的抗高温氧化性及硬度,而加入B等元素可提高涂层的硬度和附着强度。
由于多组元成分的复杂性,对此研究也存在很多争议.在对(Tix,Cr1-x)N多组元涂层的研究中,研究结果存在较大争议。有人认为(Tix,Cr1-x)N涂层是以TiN为基,Cr只能以置换固溶体的形式存在于TiN点阵中,而不能作为独立的CrN相存在[11];另外一些研究表明:(Tix,Cr1-x)N涂层中Cr原子直接置换Ti原子数量有限,其余的Cr则以单质态存在或与N形成化合物。相关实验结果表明:涂层中添加Cr能减小表面颗粒尺寸,提高硬度,当Cr的质量百分含量达到3l%时,涂层硬度达到最高值,但涂层的内应力也达最大值。
3其他涂层
除常用的TiN涂层外,还有许多不同工程陶瓷被应用在齿轮表面强化上。
(1)日本Y. Terauchi 等研究了用气相沉积法沉积碳化钛或氮化钛陶瓷齿轮的抗摩擦磨损的能力。齿轮在镀覆之前,进行了渗碳和抛光处理,使齿轮表面硬度达到HV720左右,表面的粗糙度为2.4μm,碳化钛陶瓷涂层通过化学气相沉积法(CVD)制备,氮化钛用物理气相沉积法(PVD)制备,陶瓷膜层厚度约为2μm。通过在有油和干摩擦的情况下分别研究其摩擦磨损性能,发现镀覆陶瓷涂层后齿轮副的抗咬合性和抗划伤的能力得到大幅增强。
(2)化学镀Ni-P与TiN的复合涂层通过预涂Ni-P作为过渡层,再沉积TiN制备复合涂层。研究表明,这种复合涂层表面硬度得到一定程度的提高,涂层与基体结合较好,并且具有较佳耐磨性。
(3)WC/C,B4C薄膜日本技术学院机械工程系M. Murakawa等人利用PVD技术在齿轮表面沉积WC/C薄膜,在无油润滑的工况下,其使用寿命是普通淬火磨削齿轮的3倍;Franz J等利用PVD技术在FEZ-A和FEZ-C齿轮表面沉积WC/C与B4C薄膜,实验表明:PVD镀层显著减少齿轮摩擦,使齿轮不易出现热胶接或胶合,提高了齿轮的承载能力。
(4) CrN薄膜 CrN薄膜与TiN薄膜类似,都具有较高的硬度,而且CrN膜抗高温氧化性比TiN强,耐蚀性较好,其内应力较TiN膜层低,且韧性相对较好。陈灵等[20]在高速钢表面制备出具有优异膜基结合力的耐磨TiAlCrN/CrN复合膜,还提出了多层膜的位错堆积理论,若两层膜之间的位错能量区别较大,则发生在一层的位错将难以穿过其界面进入另一层,从而在界面处形成位错的堆积,起到强化材料的作用。钟彬等[21]研究了氮气含量对CrNx薄膜相结构及摩擦磨损性能的影响,研究表明,随着N2含量的增加薄膜中Cr2N(211)衍射峰逐渐减弱,CrN(220)峰逐渐增强,且薄膜表面大颗粒逐渐减少,表面趋于平整,当N2通气量为25ml/min时(靶源弧流为75A,负压100V)沉积出的CrN薄膜具有良好的表面质量、较好的硬度和优良的耐磨性能。
(5)超硬膜 超硬膜指硬度大于40GPa、具有优异耐磨、耐高温性和低摩擦系数、低热膨胀系数的固体薄膜,主要是非晶金刚石膜和C-N膜。非晶金刚石膜具有非晶特性,没有长程有序结构,含有大量C-C四面体键,所以也被称为四面体非晶碳膜。类金刚石涂层(DLC)作为一种非晶碳膜,具有诸多类似金刚石的优良特性,如热导率高、硬度高、弹性模量高、热膨胀系数小、化学稳定性好、良好的耐磨性和较低的摩擦系数等。有研究表明在齿轮表面涂覆类金刚石膜可以延长6倍使用寿命,抗疲劳性能也有显著提高[22]。C-N膜,又称无定型碳氮膜,其晶体结构类似于β-Si3N4共价化合物,因此也被被称为β-C3N4。Liu和Cohen等从第一性原理出发,采用赝势能带计算法进行严格的理论计算,确认β-C3N4具有较大的结合能,力学结构稳定,至少能一亚稳态存在,并且其弹性模量与金刚石相当[23],性能良好,能有效提高材料表面硬度和耐磨性,降低摩擦系数。
(6)其他合金耐磨涂层 一些合金耐磨涂层也被尝试应用在齿轮上,例如在45#钢齿轮齿面沉积Ni-P-Co合金层,是合金层获得超细晶粒组织,可延长接触疲劳寿命达1.144~1.533倍。还有学者研究在Cu-Cr-P合金铸铁齿轮齿面涂镀Cu金属层和Ni-W合金涂层,提高其接触疲劳强度;在HT250铸铁齿轮齿面上涂镀Ni-W和Ni-Co合金涂层,与未涂镀的齿轮相比,耐磨性提高4~6倍。
——文本由真空镀膜设备厂家广东918博天堂科技发布